SAINT-LOUIS CRYSTAL || Mouth-Blown, Hand-Crafted Glass Creations Since 1586

It takes a village.
This is what we realized after we had a behind the scenes look at Saint Louis Crystal’s creative process. Known for outstanding craftsmanship and design, Saint-Louis Crystal’s enchanting and luxurious handmade items encompass the work of its team of dedicated artisans. The brand has a fascinating history and is renowned as the oldest glassmaking manufacturer in Europe since 1586.
Through the centuries, the brand’s designs and collections have evolved to include a range of homeware including tableware, furniture, lighting design, and more. Saint-Louis Crystal has produced many cherished collectibles, including beautiful ‘Hulotte’ pendant lights, fantastical chandeliers from the Arlequin collection, and even a collaboration with The Palace of Versailles. Still nestled in the forests of Moselle, the Saint-Louis manufacture workshop, where some craftsman are 7th generation, offers a glimpse into the masterful craftsmanship of the brand’s stunning pieces.
The creation of mouth-blown and hand-made glassware has been a collective effort
We had the pleasure of interviewing the Saint-Louis Crystal team to gain a deeper understanding of the brand’s history, commitment to industry-leading craftsmanship, and innovative collaborations.
S: Saint-Louis Crystal
P: Pendulum Magazine
P: Saint-Louis Crystal began in 1586 in the eastern French forest of Moselle and the workshop is still nestled in its place. Does this location provide inspiration for the stunning pieces created by the brand both past and present?
S: Favored by sixteenth-century itinerant glassmakers for its rich resources – silica sand, potash from ferns, firewood, and river water – the Saint-Louis forest is also fertile territory for the imagination. The spirit of the Vosges channeled its energy into the glassmaker’s breath that transforms magma into crystal: the wood and ferns once fired its kilns, the flowers and the colors drive inspiration.
The Folia collection designed by Noé Duchaufour-Lawrance for Saint-Louis is directly inspired by these surroundings. The first cross-disciplinary collection for the House expresses the vibrant alliance of crystal and wood, simple lines, and modern usage. Each piece in the collection is decorated with organic cuts, in homage to the leaves in the Moselle woodland. A new extension of the portable lamp debuting in 2021 pays homage to the encounter between the sparkle of crystal and the strength of wood, so dear to the message of the Folia collection.
“The idea for the Folia portable lamp was born during a walk in the forest with Noé Duchaufour-Lawrance on the outskirts of the factory. We were talking about the magic of a picnic surrounded by fireflies. In our rather romantic musings the notion of a roaming light appeared authentic against the backdrop of the forest, where fireflies use bioluminescence to shine in the night. The lamp’s glow also guides us from house to house and reminds us of the presence of man in the Vosges forest, on the outskirts of the factory, whose heart never stops beating even when the fireflies are asleep.”
P: The Müntzthal glassworks became Verrerie royale (Royal Glassworks) in 1767 through Louis XV’s royal seal of approval. While Italy and Bohemia were producing crystalline, it was the Englishman George Ravenscroft who perfected the technique for making genuine crystal. How was this mystery solved by experts at Saint-Louis in 1781?
S: 1781 marks a historical milestone when Saint-Louis’ alchemists conquered the formula of the composition of crystal seeking to make the finest and most transparent glass possible, an enterprise encouraged by M. de Beaufort, Director at this time of the Verrerie Royale de Saint-Louis. In 1782, the Saint-Louis crystal formula was recognized by the Academy of Sciences and the manufacture officially became the Cristallerie Royale de Saint-Louis. The exact composition of Saint-Louis crystal is confidential and has been kept as a secret ever since. Each crystal factory has its own recipe, and Saint-Louis’ is acknowledged as the French-made finest.
Artisan carefully examining each piece to guarantee perfection
P: What is unique about the design and production process at Saint-Louis Crystal? Are there specific qualities on a finished piece that identifies it as a Saint-Louis piece?
S: Saint-Louis signs every crystal creation – lighting, tableware, decorative pieces and furniture – crafted by master glassblowers and cutters who are considered to be among the very best in France (“Meilleurs Ouvriers de France”). All possess irreplaceable knowledge and ancestral skills that have been enriched from generation to generation: crystal is mouth-blown, hand-cut, hand-engraved and hand-decorated using 24-carat gold or platinum. Using these skills, they established Saint-Louis as the master of colors and cuts.
With a range of over 10 shades, either mass-colored or cased, and a multiplicity of cuttings from the emblematic diamond pattern, to bevels through pearl, olive, star and cord cuts, the brand offers a large variety of styles and exceptional creations.
Saint-Louis is truly a manufacturer ahead of its time, a blend of tradition and innovation that never ceases to draw inspiration from contemporary artistic trends in order to renew and shape its identity.
Artisan working a Hulotte pendant light
P: What are some of the largest changes to the company as a whole in terms of strategy? On the other hand, what are the core values that have been preserved over the centuries?
S: Originally acknowledged for tableware, Saint-Louis continues to give priority to the development of lighting - contemporary and timeless - by relying on its two strengths: semi-bespoke & customization and by diversifying the typologies of lighting: a modular and customizable system, chandeliers of various sizes, and a portable lamp to meet all uses and be taken everywhere. Saint-Louis added lighting to its product range in 1837. Since then, the manufacture offers almost infinite customization possibilities! Saint-Louis offers a customized version of ready-to-light collections as well.
Over the years, Saint-Louis has become a master in the art of fulfilling its customers’ wildest dreams, even building a chandelier of more than 9 meters tall. Mark your calendars: in September 2021, Saint-Louis will come back in Brera for the Euroluce edition of Salone del Mobile in Milano.
Saint-Louis has always been a manufacturer ahead of its time, a blend of tradition and innovation that never ceases to draw inspiration from contemporary artistic trends to renew and shape its identity. In the wave of creativity that swept through the early 20th century, between Art Nouveau and Art Deco, external designers brought their talents to bear at Saint-Louis, artists such as Paul Nicolas, Jean Sala, Jean Luce, Michel Colle and Maurice Dufrêne, to name but a few.
2021 sees a reissue of prestigious decoration pieces in celebration of Saint-Louis exceptional Heritage: a Jean Sala vase presented by Saint-Louis at the Paris universal exhibition of 1937, the Guipure and Tartan vases from 1940-1950, These prestigious pieces illustrate a fascinating juxtaposition of age-old heritage with a radically contemporary aesthetic.
Craftsman taking extreme care in installing a Saint-Louis Arlequin chandelier
P: Understanding that the creation of pieces involves a fierce battle between heavy matter and time because crystal hardens at room temperature, what are some ways that craftsmen build on the technique of these well-rehearsed movements passed down through the ages?
S: It takes many years of training to master the fire and acquire this ancestral know-how. In the ambient heat of the roaring furnaces, the material enters a molten state, and the Saint-Louis glass-blowers shape and blow the crystal. Given the urgency of the hardening material, this endlessly repeated dance requires precise gestures. The effervescent atmosphere of this hive of activity highlights the perfect coordination of the glass-blowers. Everyone plays their role, all working together. The gatherer collects the formless material and hands it to the gaffer, who then shapes it. The latter gives life to the object, before removing it from his blowpipe. The carry-in assistant then places the piece in the annealing furnace for a few hours. Every piece created by Saint-Louis is the fruit of an intense collective effort, flawlessly orchestrated by age-old gestures that have been passed down since 1586.
Shaping the crystal
P: Can you go into more detail about the difference between the hot-glass and cold-glass workshops? How have the workshops, and perhaps craftspeople evolved over time?
S: At Saint-Louis, the hot workshop is the essence of the central hall since it is where the crystal glass is produced under high temperature. It is in the heart of the continuous casting furnace that the melting of the crystal takes place at 1450 ° C in the form of a malleable incandescent lava free of all its impurities before being deposited in the sampling zones. Then, in “collecting bays” maintained at a constant temperature of 1200 ° C, the glassmakers “pick up” the crystal quantity necessary to produce a unique piece at the end of their cane from the glass to the chandelier branch. After this, they place the molten glass in a mold of beech wood or steel, where, in a fury of flames and steam at 900°C, the initial form of the object, the parison, is pressed. Finally, working in small groups, the glassworkers perform a series of rapid sequences in which the eye, the hand and the mouth are the tools of the trade. There are also shears that cut, trim and open; wooden pallets that fashion and straighten; pincers that hold, stretch and twist; but the glassblower’s skill lies in his ability to blow and turn the rod at the same time while measuring the effects on the crystal, now at 600°C.
Contrary to the hot workshop, the cold workshop imparts a studious atmosphere. It is where the crystal is cut. From the star-shaped cut to the iconic diamond cut, the work of the master cutter is above all that of a decorator. The “cold” is a craft of art and excellence: gestures are refined, constantly perfected - from 30 to 35 interventions are necessary for a glass engraved and decorated with fine 24-carat gold. After that, the piece is engraved with acid and decorated with gold or platinum by brush and hand only. After a meticulous choice and examinations under the eye of selectors, Saint-Louis can affix its signature.
P: What approach has the brand taken to balance commercial needs with artistic innovation in your creations?
S: It is thanks to its hereditary ability to adapt and constantly innovate that Saint-Louis has skillfully sidestepped any risk of being engulfed by fashion or trends and to keep a balance between commercial needs and artistic innovations. Saint-Louis offers a broad range of products, from affordable gift to exceptional pieces.
Also, today, Saint-Louis continues to call on the imagination and skills of designers who open the way to new uses for crystal – and so the tableware, decorative object and lighting collections are enriched by the creations of Eric Gizard, Hervé van der Straeten, Ionna Vautrin, José Lévy, Kiki van Eijk, Noé Duchaufour-Lawrance, Paola Navone. For existing within one’s time also means escaping the ephemeral.
P: Take us through the design process of how Saint-Louis comes up with a new product.
S: Through the workshops of the Saint-Louis studios, the object embarks on a crazy adventure with the craftsmen and carries with it a succession of events. The object, imagined by the designer from the nonexistent, is then formed by the ephemeral breath of the glassmaker, the virtuosity of the mason, the patience of the mold-maker smoothing the surfaces of a matrix.
At Saint-Louis, each product holds a story. For the Matrice collection, Kiki van Eijk (a designer from the Eindhoven Academy) has repurposed the use of the molds of the manufacture. Inspired by the warehouse that stores molds and casts, Kiki wanted to shine a light on these tools from which all of Saint-Louis’ creations originate. She gave every object in the Matrice collection the unique shape of a mold, adorning each one with the hand-cut elements (diamonds, bevels) that are the signature style of the company. The unusual aesthetic of this collection shares the story of its own production process. This collection expresses a fascination for fire and for molten materials, the marriage of traditional expertise and technology, of work and light.
P: Which collection(s) is Saint-Louis Crystal most proud of, and why?
S: Saint-Louis nurtures its most beloved creations. Some collections are already iconic such as Tommy and Royal. Yet, while the crystal manufacture has its imposing looks, no one look is ever imposed. “There is not one Saint-Louis style, but many,” CEO Jerome de Lavergnolle likes to say.
More than a look, Saint-Louis offers experiences. Saint-Louis has collaborated with the most prestigious institutions and luxury brands through the realization of exceptional pieces. Saint-Louis and the Comédie-Française created side by side a classic 85-light chandelier for the Mounet-Sully salon, restored in 2017. Inspired by an engraving from Pierre Fontaine dating back to 1830, the masterpiece is mouth-blown and hand-cut. A bold, precise cut, strong, euphoric colours, extremely refined designs, and materials: this is the clear identity that Saint-Louis perpetuates in its crystal collections.
However, if only one collection had to be chosen, Tommy would be the most emblematic. Designed in 1928, the Tommy service made an impression in 1938 during an exceptional lunch held in Versailles. Over two hundred guests were present including the King of the United Kingdom George VI and Queen Elizabeth. From its star-shaped base to its parison adorned with diamond, bevel, pearl, and rim cuts, Tommy reflects all the dexterity of the glass masters of Saint-Louis. Having become an iconic collection, it makes the best sales, all colors and countries combined, all over the world, within the Saint-Louis network as well as on the brand's e-shop.
We want to thank Saint-Louis Crystal for sharing the brand’s story with us. The process of how the brand’s luxurious and timeless pieces are made is truly fascinating. While the end result, a delicate crystal work of art sitting atop your kitchen counter, may look simple and classic, a tremendous amount of work and effort goes into handcrafting each piece.
The Saint-Louis Crystal story demonstrates how a brand’s continued success is the result of a collective effort, comprising of visionary leadership to navigate changing economic conditions, and also the passing down of masterful skills to artisans from one generation to the next.
Photos courtesy of Saint-Louis Crystal
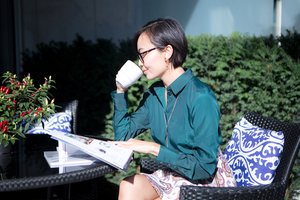